Chemical reactors
The design of a reactor is determined by many factors but the most important are the thermodynamics and kinetics of the chemical reactions being carried out.The two main types of reactor are batch and continuous.
1) Batch reactors
Batch reactors are mostly used for the reactions being carried out in a laboratory with the reactants being placed in a test-tube, flask or beaker. They are mixed together, often heated for the reaction to occur and then cooled. The products are poured out and purified if necessary.This procedure is also carried out in the industrial scale with the key difference being one of size of reactor and the quantities of reactants.
The following image shows a batch reactor.
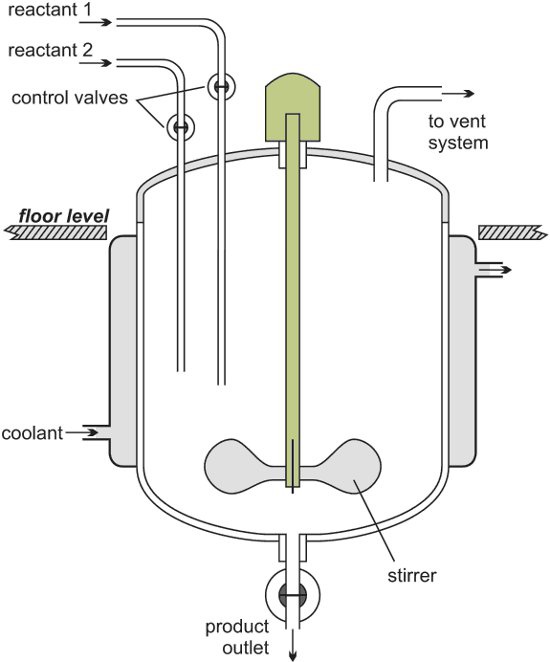
After the reaction, the reactor is cleaned to ready it for another batch of reactants to be added.
Batch reactors are usually used when a company wants to produce a range of products involving different reactants and reactor conditions. They can then use the same equipment for these reactions.
Examples of processes that use batch reactors include the manufacture of colorants and margarine.
2) Continuous reactors
Alternatively, the reactant feed can be fed continuously into a reactor at one point, then the reaction occurs in the reactor and the product and byproducts withdrawn from another point. The inlet flow must he equal to the outlet flow.Softening hard water is an example of a continuous process. Hard water is passed through a tube containing an ion-exchange resin. The reaction occurs down the tube and soft water pours out at the exit. This is summarized below:
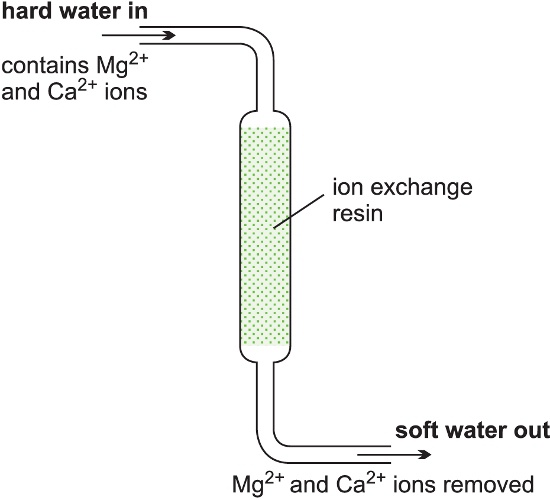
Continuous reactors are general used to produce large quantities of a chemical and needs to operate for several months without a shutdown.
The residence time in the reactor is controlled by the amount of reactant fed into the reactor. Since the volume is fixed, the residence time in the reactor is easy to control.
The products from a continuous process tend to have a more consistent quality since the reaction parameters like residence time, temperature and pressure are easily controlled than in batch operations.
The amount of waste produced is also less and it requires much lower storage of both raw materials and products hence its a more efficient operation. This means that the capital costs per ton of product produced are lower.
The main disadvantage is their lack of flexibility as the reactor built is rarely used to perform a different chemical reaction.
There are several types of continuous reactors:
(a) Tubular reactors
In a tubular reactor, fluids (gases and/or liquids) flow at high velocities. As the reactants flow along a heated pipe, they are converted to products. At these high velocities, the products are unable to diffuse back and there is little or no back mixing. The conditions are referred to as plug flow. This reduces the occurrence of side reactions and increases the yield of the desired product.With a constant flow rate, the conditions at any one point remain constant with time and changes in time of the reaction are measured in terms of the position along the length of the tube.
The reaction rate is faster at the pipe inlet because the concentration of reactants is at its highest and the reaction rate reduces as the reactants flow through the pipe due to the decrease in concentration of the reactant.
Tubular reactors are used, for example, in the steam cracking of ethane, propane and butane and naphtha to produce alkenes.
(b) Fixed bed reactors
It is described as a fixed bed of catalyst. A heterogeneous catalyst is used where gases flow through a solid catalyst (which is often in the form of small pellets to increase the surface area). The figure below shows a fixed bed reactor.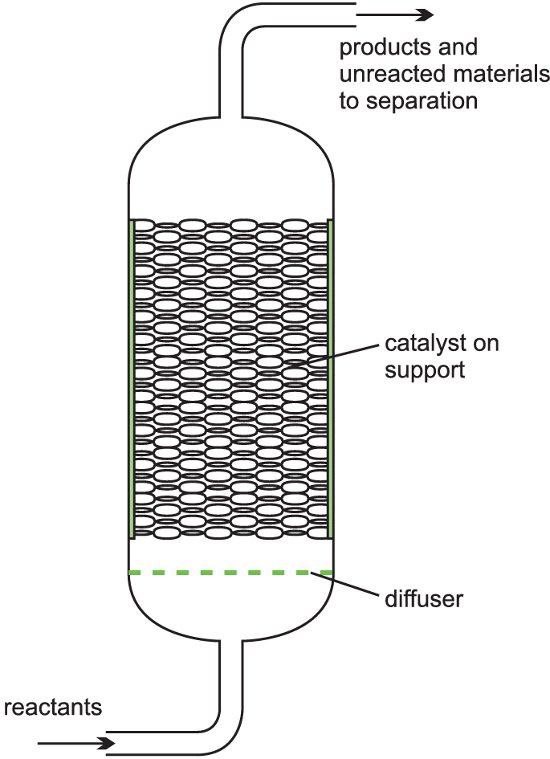
These type of reactors are used in the following processes:
- The manufacture of sulfuric acid through the Contact Process, with vanadium(V) oxide as catalyst.
- The manufacture of nitric acid.
- The manufacture of ammonia through the Haber Process, with iron as the catalyst.
- The catalytic reforming of naphtha to produce branched chain alkanes, cycloalkanes and aromatic hydrocarbons using a platinum or a platinum-rhenium alloy on an alumina support.
(c) Fluid bed reactors
A fluid bed reactor is sometimes used whereby the catalyst particles, which are very fine, sit on a distributor plate. When the gaseous reactants pass through the distributor plate, the particles are carried with the gases forming a fluid. This ensures very good mixing of the reactants with the catalyst, with very high contact between the gaseous molecules and the catalyst and a good heat transfer. This results in a rapid reaction and a uniform mixture, reducing the variability of the process conditions.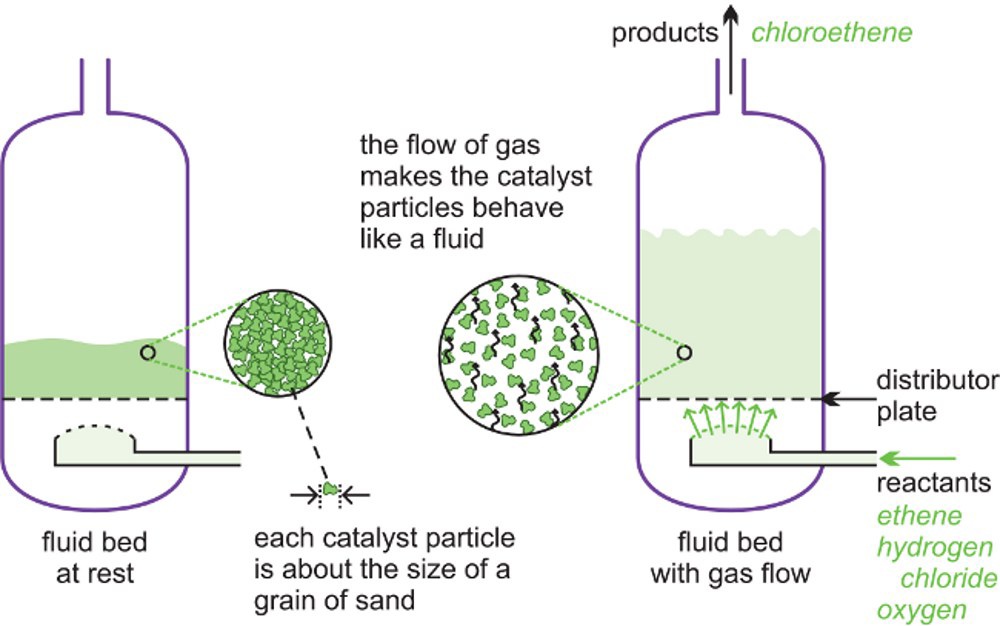
Above is an illustration of a fluid bed reactor. On the left hand side, the particles are at rest. On the right hand side, the particles are now acting as a fluid, as the gaseous reactants pass through the solid.
It is used in the following processes:
- The oxychlorination of ethene to chloroethene (vinyl chloride)
- The feedstock for the polymer poly(chloroethene) (PVC). The catalyst is copper(II) chloride and potassium chloride deposited on the surface of alumina.
- The catalytic cracking of gas oil to produce alkenes (ethene and propene) and petrol with a high octane rating.
These reactors are larger than fixed bed reactors and are more expensive to construct. However, it is easier to control the conditions and the process is more efficient.
(d) Continuous stirred tank reactors, CSTR
In a CSTR, one or more reactants are introduced into a reactor equipped with a stirrer and the products are removed continuously. The reagents are stirred vigorously for good mixing to ensure there is a uniform composition throughout. The composition at the outlet is the same as in the bulk in the reactor. These are exactly the opposite conditions to those in a tubular flow reactor where there is virtually no mixing of the reactants and the products. The figure below shows a CSTR.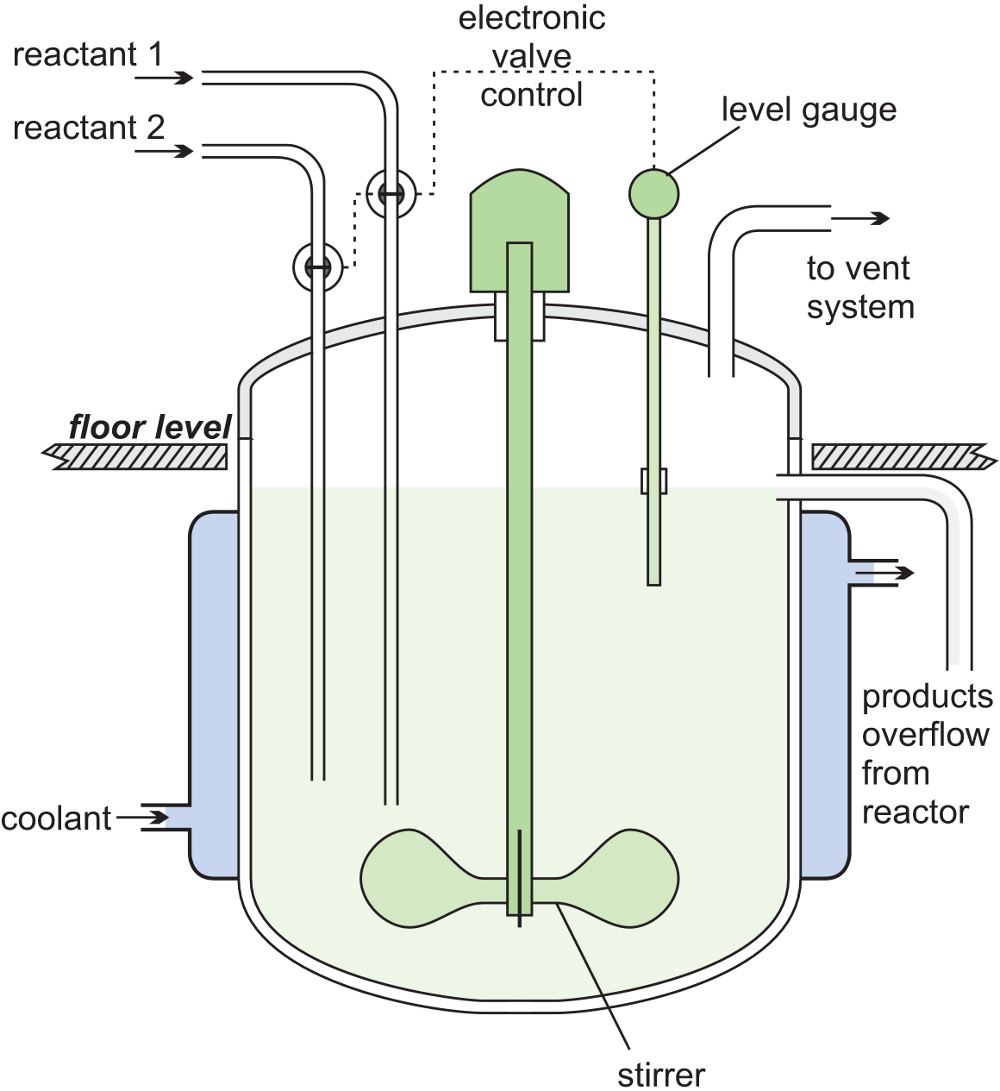
A steady state must be reached so that the flow rate into and out of the reactor are equal or the tank would empty or overflow. The residence time is calculated by dividing the volume of the tank by the average volumetric flow rate.
A CSTR reactor is used in the production of the amide intermediate formed in the process to produce methyl 2-methylpropenoate.
A variation of the CSTR is the loop reactor which is relatively simple and cheap to construct. These are used in the manufacture of poly(ethene) and poly(propene).
Future of reactors
Microreactors are the future of chemical production where the size of a reactor is about the size of a desktop computer. The reduced size will lead to reduced capital costs and reduced amount of chemicals used at any one time resulting in safer processes.The temperature can be kept constant easily due to larger surface area for a volume allowing more efficient heat transfer to the surroundings even for exothermic reactions.
There is considerable amount of research being carried out in developing microreactors. One example is the possibility of the direct conversion of benzene to phenol. A mixture of benzene and oxygen is fed through an alumina tube, packed with palladium at 350-400 K and hydrogen gas is passed over it. The figure below shows a microreactor being used to produce phenol from benzene.
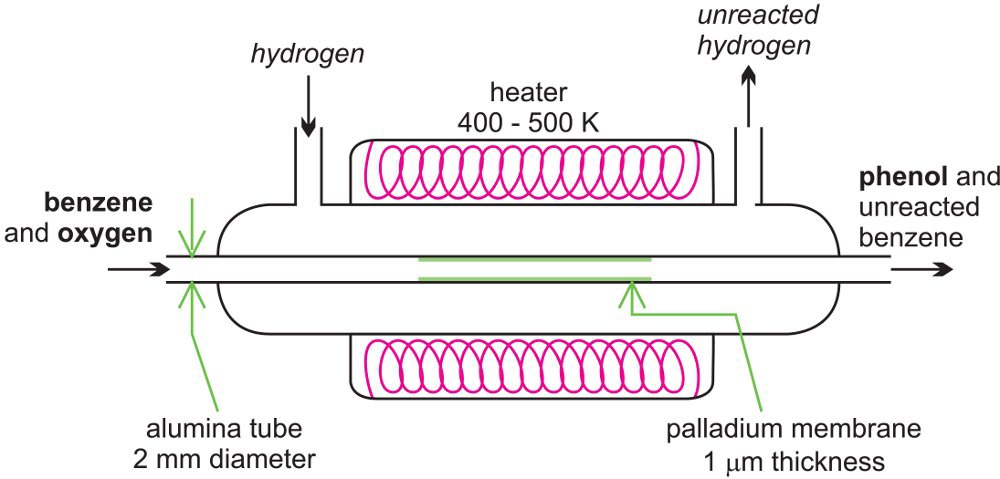
Hydrogen permeates through the alumina tube, and is converted to atomic hydrogen by the palladium catalyst. The hydrogen atoms react with oxygen, releasing reactive oxygen species, such as hydroxyl radicals, which in turn react with the benzene to form phenol.
Another development is known as oscillatory flow mixing. Chemical engineers are designing reactors where the fluids to be reacted are oscillated inside a reactor with baffles at frequencies between 0.5 and 15 Hz with amplitudes in the range 1 to 100 mm. This allows for very effective mixing of the reactants and also for heat to be transferred to the surroundings. This gives similar conditions to those in plug flow which are otherwise difficult to achieve with small quantities of materials.
No comments:
Post a Comment